esw GROUP AI-supported ticketing system for technical faults
Digitalization for industry – The challenge of knowledge transfer
Among the most pressing problems currently facing Germany’s mid-sized companies is a shortage of skilled workers. This issue is slowing down critical processes in multiple areas, including maintenance. At the same time, companies’ repositories of valuable technical knowledge are in danger of being lost as older employees retire. The esw GROUP, which specialises in manufacturing high-quality metal and metal-plastic components for industries like the automotive sector, is meeting these challenges in a variety of ways, one of which is its own digitalisation strategy.
As part of the Service Master research project, which focuses on the development of a comprehensive, AI-based service platform for German mid-sized companies, the esw GROUP and IT project experts inovex worked together to create a solution which harnesses the potential of AI to optimise collaboration between machine operators and service technicians in production. The new cloud-native application facilitates and systematises access to relevant malfunction and repair data, aids in the creation of precise fault descriptions, and correctly categories problems occurring in machinery. It then suggests potential solutions based on both the current input and historical data, thereby avoiding unnecessary downtime and expense.
AI strategie replaced Excel
The long-established esw GROUP – or, to give it its full name, Eichsfelder Schraubenwerk GmbH – is headquartered in Heilbad Heiligenstadt, in Germany’s Thuringia region. The family-run company uses a range of different manufacturing processes, such as cold forming and stamping, to produce components for multiple key industries. With around 340 employees in Germany and the Czech Republic, the group manufactures and sells fasteners which are used, for example, in almost every make and model of passenger vehicle, including in engine compartment locks, in door check and belt tensioner systems, and in parking brakes. The group produces more than 150 million such parts annually.
In order to manufacture the company’s extensive product range, the group’s equipment operators work on a wide variety of machines. Some of these have proven themselves over decades, while others are state of the art. Until now, any problems which arose could only be resolved by experienced employees. This meant that both younger workers and newer machines could quickly find themselves standing idle if no colleague with the requisite knowledge was available. An Excel file containing macros was used for maintenance tasks, as well as to document and classify problems and identify solutions. As part of its new AI strategy, the esw GROUP was seeking a more streamlined, future-proof tool with added value, and they contacted inovex’s digitalisation experts in 2022.

Making data useful; eliminating sources of error
The new application, which was developed jointly with inovex, optimises the maintenance processes in the esw GROUP’s production facilities. The esw GROUP’s existing data on previous technical malfunctions in production equipment, associated technology, and plant technology – 18,000 data records to date – has been enriched by AI and made directly accessible at any time. Intelligent algorithms and an extremely intuitive user interface (UI) make the application usable by all employees, regardless of their computer literacy level.
The unique input screens enable machine operators to describe the current problem very precisely and in natural language. Employees with limited experience of fault reporting can draw on the new application’s automated suggestions and guidance. The AI then categorises the malfunction, enabling the appropriate maintenance team – such as the electrics or pneumatics section, for example – to be contacted directly via the UI. This prevents the wrong department from being contacted accidentally, saving costs and valuable resources.
Initially, the AI application requires human oversight, and experts carefully evaluate the automated system’s work. The system also benefits the maintenance experts themselves: if a particular machine has already been repaired, the experts can access the relevant documentation. This can then be searched and the appropriate information retrieved, allowing the fault to be repaired based on previous reports.
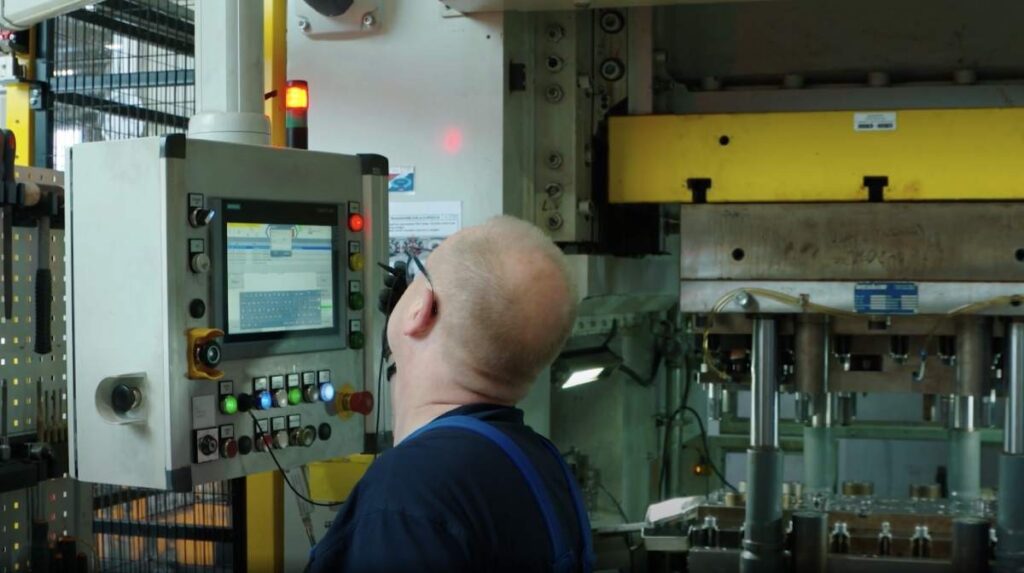
From research to practice
For the one-year research project, which was funded by the German Federal Ministry for Economic Affairs and Climate Action, inovex assembled an interdisciplinary team of students and permanent employees. This team worked with esw GROUP’s experts both remotely and on site and furnished numerous ideas over and above the purely technical aspects involved. On the inovex side, two front-end team members and one machine-learning (ML) team member worked on the front and back ends, with additional support provided by an inovex data scientist. In an initial on-site workshop, the inovex experts carefully studied the current issues, as well as the esw GROUP’s existing database, in order to develop a use case.
Soon after the initial project meeting, the inovex team was able to present a functioning front end. Two additional on-site visits by the inovexperts to the esw GROUP focused primarily on increasing its user friendliness and studying the environment of the emerging solution. In June 2023, less than twelve months later, the final operational application was unveiled. The resulting solution is set to replace the old, Excel-based solution and its macros any day now, and additional application scenarios are currently being researched.

The technology: Cloud-native, modular, and containerised
The new application was implemented cloud natively, while the back end was realised using Python. Its cloud-native implementation means that the application can be rolled out in any of the major clouds. Its modular, containerised structure, however, means that it can also easily be deployed and used in a company’s own intranet (with Docker, for example). The cross-platform development of the UI is based on Flutter, Google’s open-source development kit. For this particular case, the UI was optimised for use on desktop computers, but it can be modified to suit the needs of a variety of different projects.
The solution’s two key components are its intelligent search and its ML-based data categorisation function. The intelligent search compares the current service ticket with existing data. In doing this, it uses NLP (Natural Language Processing) models to support intuitive operation and handle heterogeneous input. In creating the solution, the inovex experts were able to draw on their experience gained from previous sub-projects in the Service Master research project, among others. Various models of the modular search system have been trialled. While a small model is sufficient for the smaller scope of the esw GROUP research project, large GPT models could, in future, be used for more complex application scenarios. The application’s machine-learning classification function categorises the faults into suitable groups. It uses unsupervised learning based on the vectorised service tickets to identify the most frequently occurring problems, as well as those most similar to each new case. Despite its complex background technology, every user-facing aspect of the application is user-friendly and intuitive.
The infrastructure-as-code deployment was implemented using Terraform, and versioning of the models ensures the traceability, the reproducibility, and thus, the optimisation of the application. ML lifecycle management is carried out through MLFlow. A role-based authentication system secures the application against unauthorised access.
“The main added value of the solution developed jointly between the esw GROUP and inovex GmbH is that it harnesses our employees’ experience and enriches it with algorithms to produce practical recommendations for action. The quality and value of our data has increased, and the new tool ensures that both plant operators and maintenance staff are deployed more efficiently.”
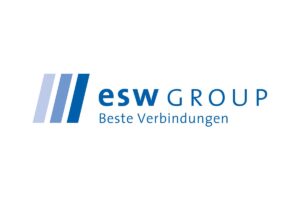
Success and potential
The result of the collaboration between the esw GROUP on the application side and inovex on the technology side is a fully operational AI-supported ticketing system. This solution crystallises the research results into an eminently practical solution which speeds up the troubleshooting process. The application is currently being tested in the field by the esw GROUP, and deployment in live operations is planned for the foreseeable future. The esw GROUP’s AI strategy anticipates both further developing the tool and extending its application to other areas – including those outside technology, such as administration.
In this joint research project, inovex showcases its many years of expertise in digitalising and optimising work processes in Industry 4.0, as well as its partnership-based collaboration with universities and other institutions on solutions for the digital future. The project is currently shortlisted for a presentation at the DemoDay held by the German Federal Ministry for Economic Affairs and Climate Action. A demo version of the project will also be a permanent exhibit in the Forum Digital Technologies (FDT)’s showroom in Berlin, a venue specifically dedicated to the issue of knowledge transfer from technology projects to German mid-sized companies.
The Service Master project is funded by the German Federal Ministry for Economic Affairs and Climate Action.
Dr. André Ebert
Machine Learning EngineerHello! 👋
How can I help you?